Executive Summary
HERAmbiente, Ferrara, Italy
Founded in 2009, Herambiente is Italy's largest waste disposal company. The company operates a total of 80 facilities that dispose of a combined total of 5.1 million tons of municipal and industrial waste each year. These include 7 waste to energy (WTE) facilities that generate over 600 GWh of electricity and 160 GWh of thermal energy each year. All of these facilities are ISO 14001 certified and over a third are registered under the Eco-Management and Audit Scheme (EMAS). The company provides its customers a complete range of alternatives such as incineration, composting, selection, chemical treatment, and landfill disposal, as well as integrated environmental decontamination services.
Herambiente's WTE plant in the city of Ferrara has been operational since 1993, and receives waste from the urban area and the surrounding province. The plant began with a single WTE line capable of handling 150 tons of waste per day, and two additional WTE lines were started up in 2007 and 2008 that gave the plant a 400 tons per day capacity. The heat recovered from the waste combustion process is used to produce steam that is used to generate 14 MW of electricity. Depending on seasonal demand levels, heat from this process is diverted to a dedicated heat exchanger that transfers an additional 30 MW of thermal energy as steam and hot water via a district heating system to the private residences in the local community. Other major sources of thermal energy for this network are two geothermal wells and a natural gas-fired thermal power station with seven boilers.
As part of the upgrade and expansion of the facilities at the Ferrara WTE plant, Yokogawa provided a turnkey solution that included the CENTUM CS 3000 control system, FOUNDATION™ fieldbus enabled instrumentation, and audio IP(internet protocol) and CCTV(closed-circuit television) systems. Also, under the terms of a six-year contract, Yokogawa is providing ongoing maintenance services.
The Challenges and the Solutions
1. Achieving steady operation
This WTE plant is relied on by the residents of the city of Ferrara and the province of the same name to provide a stable supply of heat and electricity throughout the year, with the exception of a one week period where the plant is shut down for maintenance. Helping to make this happen are Yokogawa's instrumentation solutions. This begins with the initial processing of municipal waste that is trucked to the facility, accurately weighed, and loaded by a crane into the incinerator. From their CENTUM human machine interface (HMI) stations in the central control room, operators are able to monitor every stage of this process by means of a MODBUS link to field devices and controllers.
The controls for the incinerator and boilers are all configured in the CENTUM CS 3000 system, ensuring the optimum execution of all processes, including incinerator startup. Here, natural gas burners operate to gradually bring the incinerator up to 850 deg C, whereupon the burners are shut down and a stoker begins feeding waste to the incinerator for sustained operation. All of these sequential procedures are automated by the rich functions of CENTUM CS 3000. The operation of the steam turbine, district air conditioning/heating, and emissions monitoring systems is also integrated with the CENTUM CS 3000 system. By scanning graphic displays that show trend data, operators are able to continually stay on top of processes throughout the plant on a real-time basis. When the main power supply is not available for some reason, the CENTUM CS 3000 system will also control the process by a UPS(uninterrupted power supply) and a diesel generator to provide backup power to the plant, ensuring uninterrupted operation year-round.
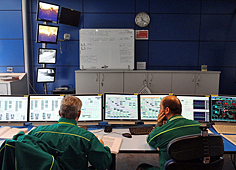
DCS-HMI stations in central control room
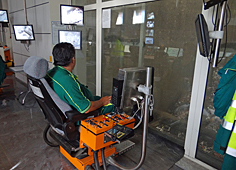
Crane operator
2. Enabling a predictive maintenance
Nearly 1,500 FOUNDATION fieldbus devices are monitored and managed using the PRM plant resource management package. Working from an engineering workstation in the central control room, engineers can check the current status of each device and modify device parameters whenever required. This reduces the need for manual checks of the devices and enables a predictive maintenance approach.
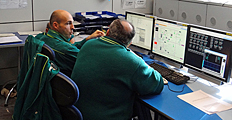
Engineering workstations
Customer Satisfaction
Plant Manager Andrea Carletti: "We are very proud of our facility and the role it plays in providing a sustainable source of energy to Ferrara city and its province. Helping to make this happen is Yokogawa's CENTUM CS 3000 system, which has operated smoothly with no major problems since it became operational in 2008."
"Our integrated system manages all processes in the Ferrara plant, from the reception of waste to the treatment of ash, from the treatment of gases from combustion to monitoring emission, from electricity production to heat production for district heating. All technical and environmental data of Ferrara plant are monitored by an integrated control system that is common to all the energy plants of the group by using a central control room. This gives the possibility to control from each remote station, the operation of each connected system. The aim of Hera group is to remotely monitor all its plants, not only waste to energy power plant. That system will be the largest in Europe. This permit to help the Hera group to achieve a higher level of efficiency in the near future."
Andrea Carletti
Plant manager
For further information
Renewable Energy:
Waste to Energy
Products & Solutions:
CENTUM (Production Control Systems)
PRM (Plant Asset Management)
FOUNDATION fieldbus (Field Digital Solutions)
業種
関連製品&ソリューション
-
適切な設備保全の実現に 統合機器管理ソフトウェアパッケージ PRM
高信頼かつ安定したプラント運転のために、適切な設備保全管理はできていますか?PRMは、プラントライフサイクルを通して設備保全計画の品質向上および設備保全コストの最適化に貢献します。